What Are Automotive Rivets Used For?
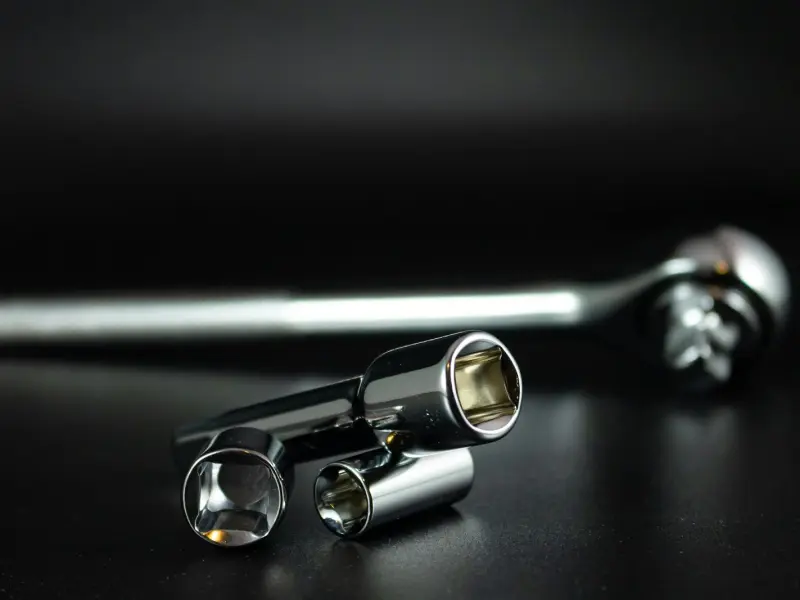
Rivets are an essential part of car manufacturing and repair, offering a simple but effective way to fasten components securely.
Automotive rivets are designed to create strong, permanent connections, whether for body panels, structural frames, or interior elements.
They’re reliable, lightweight, and versatile, making them ideal for use in vehicles where strength and efficiency are key.
If you’ve ever wondered why rivets are preferred for certain jobs or what makes them different from other fasteners, this guide will help you understand their purpose and applications.
What Are Automotive Rivets?
Automotive rivets are fasteners used to hold materials together permanently.
They consist of a cylindrical shaft with a head at one end, and when installed, the opposite end is deformed or expanded to lock the rivet in place.
Unlike screws or bolts, rivets don’t require threads or nuts, making them simpler to install in many cases.
These industrial fasteners come in various materials, including aluminum, steel, and plastic, to meet the demands of different applications.
For example, lightweight aluminum rivets are commonly used for body panel rivets, while stronger steel rivets may be needed for structural components.
Plastic rivets are often used in interior applications where durability and a clean finish are required.
What Is the Purpose of a Rivet?
The main purpose of a rivet is to create a strong, permanent joint between materials.
They’re particularly useful in situations where a fastener needs to withstand stress, vibrations, or high loads without loosening over time.
Because rivets are set into place and don’t rely on threads, they’re less likely to fail in demanding environments.
What Are Rivets Used For in Engineering?
Rivets have a wide range of applications in engineering.
They’re often used in industries like aerospace, construction, and automotive manufacturing to join parts where welding isn’t practical or where removable fasteners aren’t strong enough.
Their ability to distribute force evenly makes them ideal for structural applications, providing a secure hold without damaging the materials they connect.
What Are Rivets Used For in the Automotive Industry?
In the automotive industry, rivets are used for a variety of tasks.
They’re commonly found in assembling car bodies, attaching body panels, and securing interior components.
Auto body rivets are often chosen for their ability to provide a smooth, flush finish, which is important for both aesthetics and aerodynamics.
They’re also used in areas where vibration resistance is critical, like in frames or suspension systems.
Automotive Rivet Types
There are several types of automotive rivets, each designed for specific applications. Here are some of the most common:
Solid Rivets
These are simple and strong, often used in structural applications like joining chassis components or suspension parts.
Blind Rivets
Sometimes called pop rivets, these are ideal for situations where access is only available from one side, like fixing panels or trim.
Plastic Rivets
These lightweight rivets are perfect for interior components, offering durability and resistance to corrosion.
Tubular Rivets
With a hollow shaft, these are often used for light-duty applications or where a decorative finish is needed.
Self-Piercing Rivets
Common in modern vehicle manufacturing, these rivets don’t require pre-drilled holes and are used to join materials like aluminum and steel.
What Are the Applications of Rivets?
Rivets are used in many areas of a car’s design and construction, including:
- Body Panels: Rivets provide a clean, flush finish while securely fastening body panels to the frame.
- Interior Components: Plastic rivets are often used to attach trim pieces, dashboards, or upholstery.
- Frames and Chassis: Solid and structural rivets help strengthen the vehicle’s frame, ensuring durability and safety.
- Suspension Systems: Rivets can withstand the vibrations and forces in critical components like suspension arms.
- Exhaust Systems: Heat-resistant rivets are sometimes used to assemble or repair exhaust pipes and mufflers.
Automotive rivets are chosen for their versatility and ability to perform in environments where other fasteners might fail, ensuring a reliable connection that lasts.
Automotive Rivets: Conclusion
Automotive rivets are more than just fasteners—they’re a vital part of ensuring cars are safe, durable, and efficient.
Understanding their types and uses helps highlight their importance in modern vehicle manufacturing and repair.
When selecting rivets, choosing the right type for the job ensures a secure, lasting connection that meets the demands of any automotive application.
More Automotive Rivet FAQs
- What are the 4 types of rivets?
- The four main types of rivets are solid rivets, blind rivets (pop rivets), tubular rivets, and self-piercing rivets. Solid rivets are used in heavy-duty applications, blind rivets are ideal for one-sided access, tubular rivets suit lightweight tasks, and self-piercing rivets are common in modern car manufacturing.
- What size are car rivets?
- Car rivets typically range in size from 3.2 mm (1/8 inch) to 6.4 mm (1/4 inch) in diameter, depending on the application. Smaller rivets are often used for interior trim, while larger ones are used for structural purposes or securing body panels.
- What are rivets best used for?
- Rivets are best used for creating strong, permanent joints between materials, especially in applications where vibration resistance and durability are critical. In automotive settings, they’re used for body panels, interior trim, and structural components, providing reliable fastening without the need for threads or nuts.
- How do I know my rivet size?
- To determine the correct rivet size, measure the thickness of the materials being joined and add 1.5 times the rivet’s diameter to ensure proper grip length. Rivet size charts or guides from manufacturers can also help ensure an accurate match for your application.
- What is the minimum distance between two rivets?
- The minimum distance between two rivets should be at least three times the diameter of the rivet. This spacing prevents material stress or tearing, ensuring the rivets perform effectively and maintain the structural integrity of the joined components.
- What is the most popular rivet size?
- The most popular rivet size for automotive applications is 3.2 mm (1/8 inch) in diameter. This size is widely used for securing interior and exterior trim pieces, offering a balance of strength, ease of installation, and compatibility with various materials.
- What size hole for 3.2 mm rivet?
- A 3.2 mm (1/8 inch) rivet requires a hole slightly larger, typically 3.3 mm to 3.5 mm (around 0.130 inches). This ensures the rivet fits snugly while allowing for proper installation and deformation during setting.
- How do you calculate the number of rivets?
- To calculate the number of rivets needed, divide the total length of the joint by the desired rivet spacing (e.g., 3 times the rivet diameter). Adjust for any additional rivets required at the ends of the joint for added stability.
Resources
CNRL Fasteners uses only high-quality sources, including peer-reviewed studies, to support the facts within our articles. Our commitment to accuracy and reliability ensures that readers receive well-researched information they can trust.